Im Kampf gegen CO2-Emissionen ziehen die Gesetzgeber auf EU-Ebene die Zügel immer stärker an. Über den Finanzmarkt sowie öffentliche Auftraggeber sind alle großen Unternehmen gehalten, ihre ESG-Einstufung (Environmental, Societal, Governance, zu Deutsch: Umwelt, Soziales und Unternehmensführung) im Rahmen von regelmäßigen Überprüfungen durch spezialisierte Ratingagenturen möglichst hoch zu halten. Dazu gehört auch ständiger Druck auf die eigenen Zulieferer, ihrerseits die Einhaltung entsprechender Vorgaben nachzuweisen. Wichtiges Kriterium ist hierbei die Dokumentation des sogenannten „CO2-Fußabdrucks“. Darunter ist die Bilanzierung der im Rahmen der Unternehmenstätigkeit erzeugten CO2-Emissionen zu verstehen. Dabei geht es nicht nur um die während des eigenen Fertigungsprozesses verursachten direkten und indirekten CO2-Emissionen, sondern auch um die in den bezogenen Materialen bereits indirekt (durch vorangegangene Fertigungsschritte) enthaltenen CO2-Emissonen.
Der Konstrukteur befindet sich (auch) im CO2-Wettbewerb
Bei der Entwicklung neuer technischer Lösungen sind zahlreiche Aspekte zu beachten. In diesem Multiparameter-Umfeld muss der Konstrukteur, der sich oft im Wettbewerb mit Metallen behaupten muss, neben den ihm bekannten Gesichtspunkten wie Kosten, spezifisches Gewicht, mechanische Eigenschaften etc. heute zunehmend auch den Aspekt „CO2-Rucksack“ beachten. Bei Kunststoffen verschafft ihm dies gegenüber dem häufig anzutreffenden Aluminium im Prinzip einen nicht unerheblichen Vorteil. Um diesen jedoch voll nutzen zu können, muss er ihn allerdings auch kennen und mit Zahlen untermauern können.
Wieviel CO2 steckt in den Rohstoffen?
Bei Kunststoffen stammt der anrechenbare CO2-Gehalt zunächst einmal vom Raffinationsprozess, mit dem die Rohstoffe wie Erdöl und Naphta in den Destillationskolonnen der Raffinerien aufgebrochen und nach Siedepunkt getrennt werden. Generell gilt, dass der erforderliche Energieaufwand umso höher ist, je höhersiedend die Fraktion ist, aus welcher der betreffende Kunststoff gewonnen wird. Vom Grundsatz her schleppt somit ein Polypropylen(PP)-Werkstoff einen kleineren CO2-Rucksack mit sich herum als ein Polyamid (PA) oder gar ein Polyphenylensulfid (PPS).
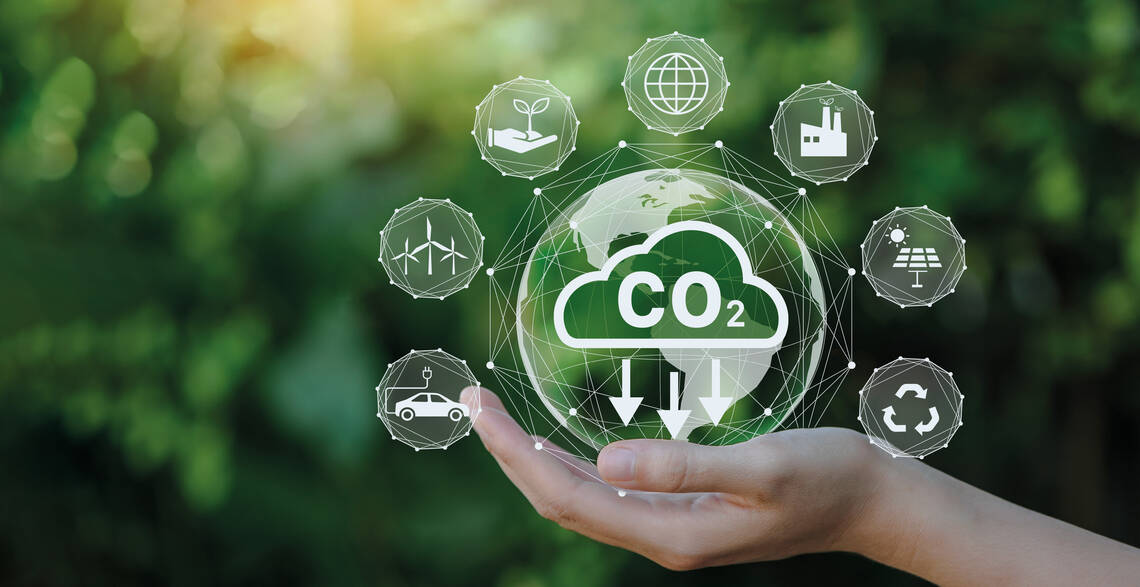
Hinzu kommt als weiterer Bestandteil der CO2-Rucksack der Energieform, welche am Standort der betreffenden Raffinerie eingesetzt wird. In einem Land wie Schweden, das seinen Strom weit überwiegend aus CO2-armen Quellen wie Wasser- und Kernenergie sowie zusätzlich etwas Solarenergie gewinnt, ist deshalb das Material weit weniger durch CO2-Emissionen befrachtet als in anderen Nationen.
CO2-Emissionen pro erzeugter kWh elektrischen Stroms in verschiedenen Ländern
- Schweden: 25 kg eCO2/kWh
- Deutschland (Mittelwert): 420 eCO2/kWh
- Niederlande (Mittelwert): 425 eCO2/kWh
- USA (Mittelwert): 430 eCO2/kWh
- Polen (Mittelwert): 625 eCO2/kWh
- Asien (Spanne): 850-1100 eCO2/kWh
Diese Differenzen – es geht um Verhältnisse von bis zu 1/44 – sind enorm. Für die Beurteilung durch den Verarbeiter kommt es allerdings zunächst auf den Vergleich der spezifischen CO2-Rucksäcke der Werkstoffe bei Herstellung im gleichen Werk an.
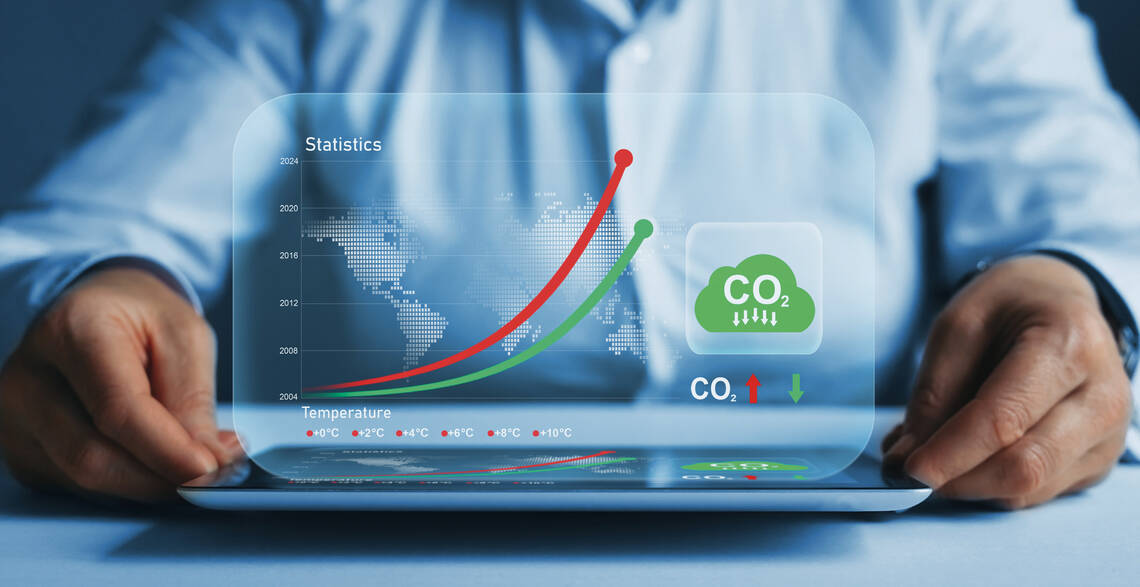
Wichtige Hebel für die Verringerung des CO2-Rucksacks
Im Prinzip gibt es vor allem vier wichtige Hebel zur Verringerung des CO2-Rucksacks des verwendeten Kunststoffs:
- Verwendung von Recyclat
- Einsatz vorteilhafterer Füllstoffe
- Substitution durch einen Kunststoff mit kleinerem CO2-Rucksack
- Beratung durch den Profilhersteller
Recyclat-Einsatz
Dies ist einer der wichtigeren Hebel, denn bei der Berechnung der CO2-Fracht wird CO2-Anteil im Recyclat als Null bewertet. Entscheidend ist hierbei natürlich, dass es sich um sortenrein erfasstes Material wie z.B. Produktionsabfälle handelt.
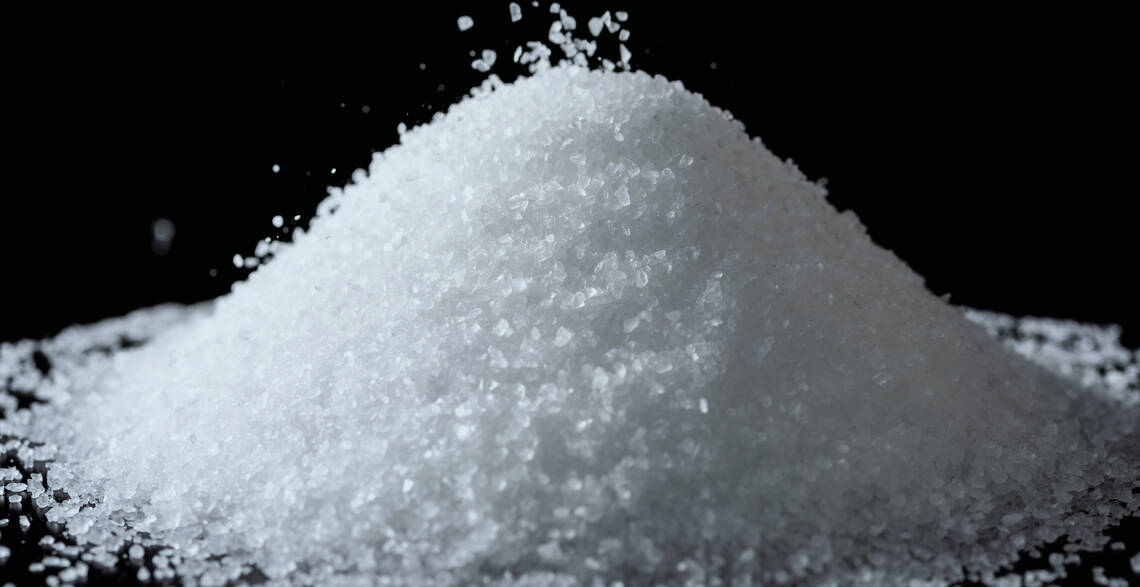
Vorteilhaftere Füllstoffe
Viele Kunststoffe enthalten mineralische Füllstoffe. Diese haben ihrerseits ebenfalls einen CO2-Rucksack, der bei der Gesamtbetrachtung unter Berücksichtigung des Fülleranteils berücksichtigt werden muss. Füllstoffe weisen teils hohe Unterschiede auf. Glasfasern haben den dicksten und Calciumcarbonat den kleinsten CO2-Rucksack.
Substitution durch einen Kunststoff mit kleinerem CO2-Rucksack
Als weiterer möglicher Hebel kann geprüft werden, ob sich der ursprünglich vorgesehene Kunststoff ohne Einbußen bei der Teilequalität durch einen kostengünstigeren Alternativwerkstoff mit zugleich schlankerem CO2-Rucksack substituieren lässt. Damit kann möglicherweise auch der Vorteil im Vergleich zu einer Aluminiumlösung nochmals ausgeweitet werden.
Entscheidend ist die Beratungskompetenz
Bei der Entwicklung neuer Kunststofflösungen ist die Werkstoff- und Prozesskompetenz des Profilherstellers heute ein immer wichtigerer Erfolgsfaktor. Deshalb findet die Entwicklung neuer Produkte heute zunehmend in gemischten Teams aus Spezialisten des Anwenders und des Zulieferers statt. Für diese partnerschaftliche Unterstützung stehen bei mobil Kunststoffprofile AG insgesamt sieben erfahrene Fachleute mit umfassender Qualifikation in den Bereichen Konstruktion, Werkstoffeigenschaften und Verfahrenstechnik bereit. Zu ihrem Rüstzeug gehört auch eine entsprechende Kompetenz bei der Berücksichtigung aller Fragen rund um die Minimierung von CO2-Emissionen.
Selbstverständlich achten wir bei unserer eigenen Materialbeschaffung darauf, deren CO2-Befrachtung möglichst gering zu halten. Wir bereiten unsere hausinternen Produktionsabfälle selbst auf und mischen sie zu einem geeigneten Anteil in die laufende Produktion derjenigen Werkstoffe ein, die wir als Recyclat anbieten. Und last but not least leisten wir mit dem äußerst CO2-armen Energiemix der Schweizer Stromerzeugung mit mehr als 60 % Wasserkraft und 35 % Kernenergie einen wesentlichen Beitrag zur Begrenzung des CO2-Budgets der Waren, die bei uns produziert werden.